AMDEC : Une méthodologie pour réduire les risques et les coûts
C’est quoi la méthode AMDEC ? Origines et concept de base
L'AMDEC ou Analyse des Modes de Défaillance, de leurs Effets et de leur Criticité, est une méthodologie mise au point afin d’anticiper et prévenir ou limiter les risques pesant sur les systèmes techniques et industriels. Autrement dit, c’est une approche qui va dans le sens de la gestion de la qualité et de la sûreté de fonctionnement.
Développée à l'origine par l'armée américaine, l'AMDEC connaît de nos jours un large succès dans divers secteurs d'activité :
- La médecine ;
- l'aéronautique ;
- l'automobile ;
- la chaudronnerie, etc.
Comme son nom l’indique, toute la méthode AMDEC repose sur la notion de mode de défaillance, c’est-à-dire aux différents scénarios de pannes possibles dans un système donné. Pourquoi est-ce si important de repérer ces modes de défaillance ainsi que les effets de défaillance qui en découlent ? Et bien tout simplement pour mieux comprendre les failles d'un composant ou d'un processus spécifique.
L’effet de défaillance se définit par l'impact que chaque défaillance pourrait avoir sur le fonctionnement global du système. Par exemple :
- Atteintes à la sécurité ;
- retards de production ;
- pertes de performance.
Dernière partie de l’acronyme et outil-clé de la méthodologie AMDEC : l’évaluation de la criticité. Celle-ci est réalisée à l’aide du NPR (Nombre de Priorité de Risque) ou alternativement en fonction de la Priorité d’Action (PA).
Le calcul du NPR prend en compte trois critères essentiels :
- la sévérité de la défaillance ;
- la probabilité d’apparition ;
- la détectabilité.
Grâce à tout cela on peut alors hiérarchiser les défaillances potentielles selon un degré de criticité défini, ce qui rend l’AMDEC essentielle dans les environnements où la précision et la sécurité sont primordiales tels que la tuyauterie industrielle, l’usinage ou la chaudronnerie.
Cette approche peut être par ailleurs renforcée par des solutions numériques, comme celle proposée par Yndia, qui offrent une précision accrue pour vos processus de gestion des projets et des risques.
Déroulement d’une analyse AMDEC : Étapes pratiques
Première étape : définir l’objectif. En effet, impossible de démarrer sur de bonnes bases sans cadrer les limites de l’analyse. Prenons l’exemple d’un procédé de chaudronnerie visant à corriger les défauts de soudure qui pourraient affecter la qualité et la sécurité des structures métalliques. Dans un tel contexte, via une approche AMDEC, on va s'attacher aux éléments spécifiques du processus tels que la préparation des pièces, les paramètres de soudage (température, vitesse de soudage, type de matériau) et les techniques de contrôle qualité.
Dans un second temps, on détermine quels sont les modes de défaillance. Ici, on va énumérer et lister les risques potentiels pour le système. Dans notre exemple de soudage, cela pourrait inclure des défauts de soudure ou des non-conformités aux normes de chaudronnerie.
Chaque risque identifié est ensuite évalué selon son niveau de criticité en calculant le NPR. Une fois de score calculé, on peut hiérarchiser les défaillances et donc décider d’un ordre d’intervention. C’est là la troisième étape.
Enfin, après ces trois étapes d’analyse, il faut tirer parti des données et des conclusions obtenues, en mettant au point un plan d’actions correctives pour chaque mode de défaillance identifié. Le but de cette étape est d’améliorer la fiabilité des procédés, en anticipant les causes possibles de défaillances et en s’assurant qu’un système de gestion adapté est en place. Des logiciels d’optimisation de l’analyse des risques peuvent également compléter l’AMDEC, notamment en accélérant la génération de scénarios de crise et en fournissant des rapports précis sur l’état actuel des risques.
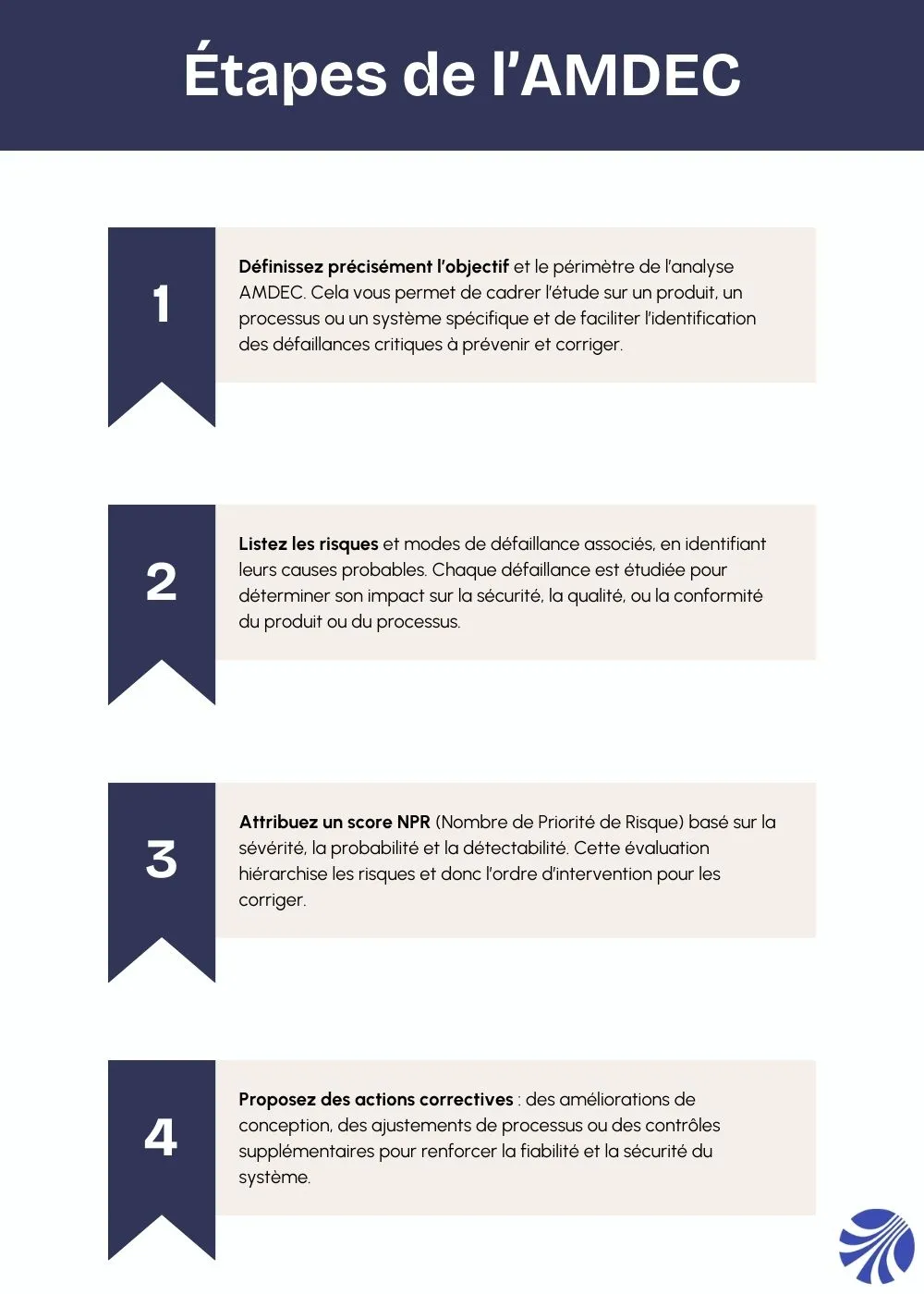
Types d’AMDEC : Appliquer la méthode à différents contextes
AMDEC Produit
L’AMDEC produit porte sur les spécifications techniques en se concentrant sur les défaillances potentielles au niveau du produit lui-même. Par exemple, lors de la conception d’une pièce d’une machine, on peut utiliser l’AMDEC pour détecter des défauts de conception et anticiper les pannes susceptibles de se produire à l’utilisation.
AMDEC Process
Ici, l’accent est mis sur les risques et la criticité liés au processus de production. Il peut s’agir de retards dans les délais de fabrication, d’une qualité trop variable des produits finis ou de problèmes de conformité réglementaire. Ce type d’AMDEC permet de sécuriser le processus de production en limitant les interruptions et en optimisant le flux de travail.
AMDEC Design
Dans cette troisième variante de la méthodologie d'analyse, on va s’intéresser aux étapes de conception et d’ingénierie. L’idée étant cette fois-ci de repérer et d’éliminer les erreurs potentielles dès le départ, avant leur implémentation au sein des process ou de la production.
Par exemple, l’AMDEC Design peut être intégrée au développement d’une cuve en métal, destinée à stocker des matériaux soumis à des normes de sécurité strictes (par exemple la réglementation DESP). Le rôle de l’AMDEC Design peut alors être de définir des limites de température pour les soudures ou de spécifier des techniques d’assemblage particulières qui permettent de mieux répartir les contraintes physiques.
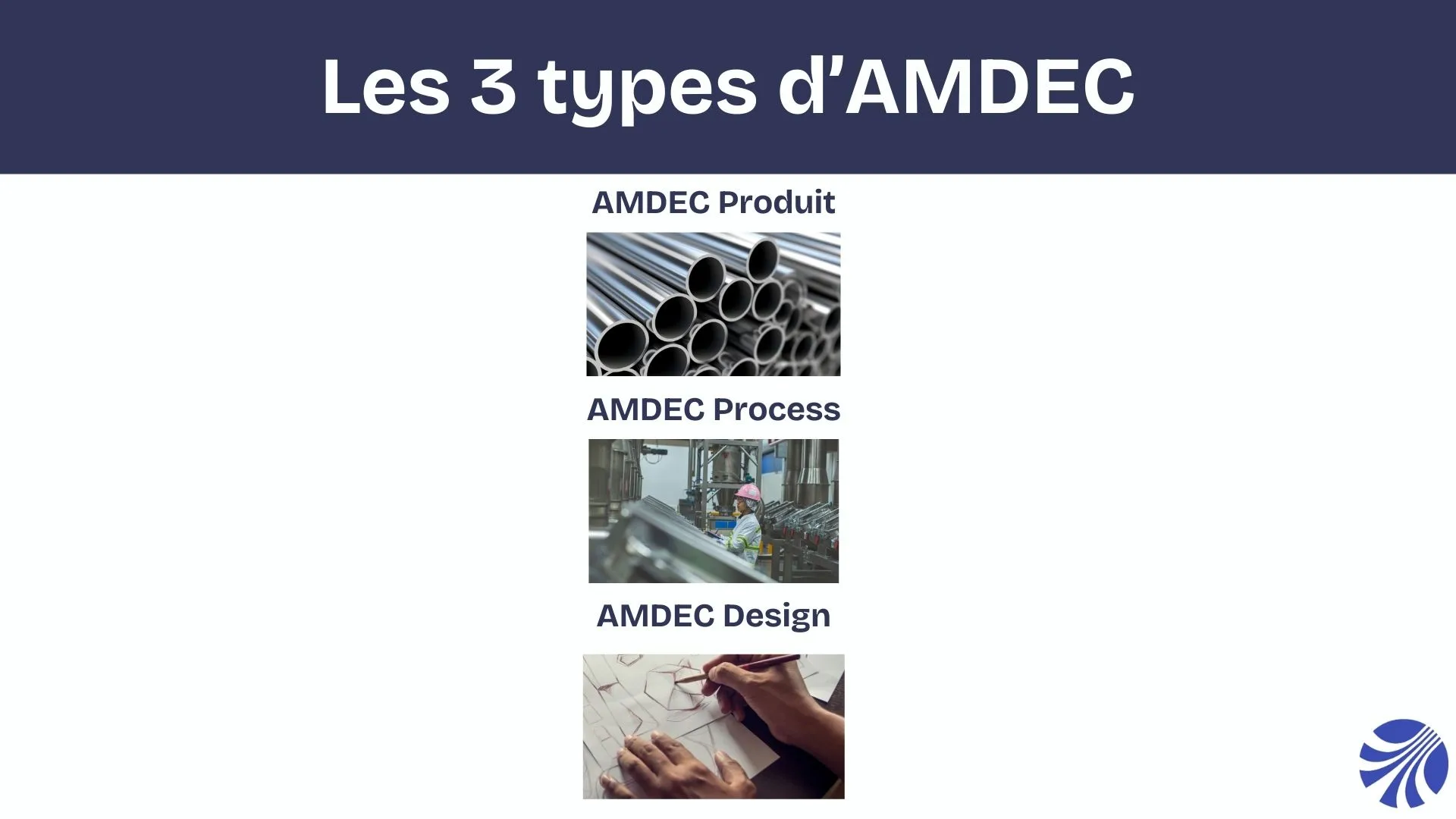
AMDEC dans un projet industriel : Stratégies et technologies complémentaires
Comment créer une stratégie de prévention des risques avec l’AMDEC ?
Pour être réellement efficace, une AMDEC doit être conduite par un groupe de travail multidisciplinaire. Ce panel d’experts fait notamment intervenir l'expertise :
- des ingénieurs qualité ;
- des chefs de projet ;
- des différents corps de métier de production (ex: monteurs, tuyauteurs, chaudronniers, techniciens en installation, etc.)
C’est grâce à la transversalité et la complémentarité des compétences qu’il devient possible de trouver les solutions les mieux adaptées.
Second volet de la stratégie : mettre l’AMDEC à contribution pour prioriser les risques en fonction de leur criticité. Un NPR élevé signifie que le risque est critique et nécessite une attention prioritaire, c’est donc vers là qu’il faudra diriger ses efforts de prévention et d’amélioration.
Enfin, notez qu'on peut structurer une AMDEC de deux manières :
- soit composant par composant (produit ou prestation) ;
- soit en suivant le déroulé du projet, phase après phase.
Dans le cadre d’une phase de conception, par exemple, l’AMDEC peut aider à anticiper les défaillances futures en se concentrant sur les éléments susceptibles de poser problème. Dans la phase de production, cette méthode permet d’optimiser le système de production en limitant les interruptions causées par des pannes ou des défauts.
Automatisation de l’AMDEC : Gain de temps et de précision
Les avancées technologiques permettent aujourd’hui d’automatiser certaines étapes de l’AMDEC, ce qui est sans conteste un gain de temps significatif pour toute entreprise.
Calcul du NPR, génération de rapports d’analyse, détection de certains modes de défaillance en temps réel, les possibilités offertes par les solutions d’analyse de risque assistée par IA sont multiples ! Chez Yndia nous l’avons non seulement compris, mais nous avons développé une solution qui fait de ces possibilités une réalité ! Renforcez la fiabilité de vos systèmes tout en réduisant les coûts associés aux inspections manuelles, prévenez les erreurs de chiffrage grâce à notre outil de chiffrage intelligent. Découvrez Yndia Dynamics !
Somme toute, la méthode AMDEC est plus qu’une simple approche pour identifier, prévenir et gérer les risques. C’est un véritable ensemble de bonnes pratiques indispensables dans une optique qualité. Étant donné que dans les secteurs où l’AMDEC est employée, la qualité est indissociable des notions de sécurité et de conformité, il s’avère qu’elle est une méthode dont on ne saurait se passer en bonne conscience. Ceci dit, elle nécessite du temps et des ressources humaines avec des équipes aux profils variés, c’est pourquoi, en automatiser les tâches les plus fastidieuses et les moins qualifiées apparaît comme un avantage de poids.