Comprendre le cycle PDCA : Un processus d’amélioration structuré
C’est quoi la méthode PDCA ?
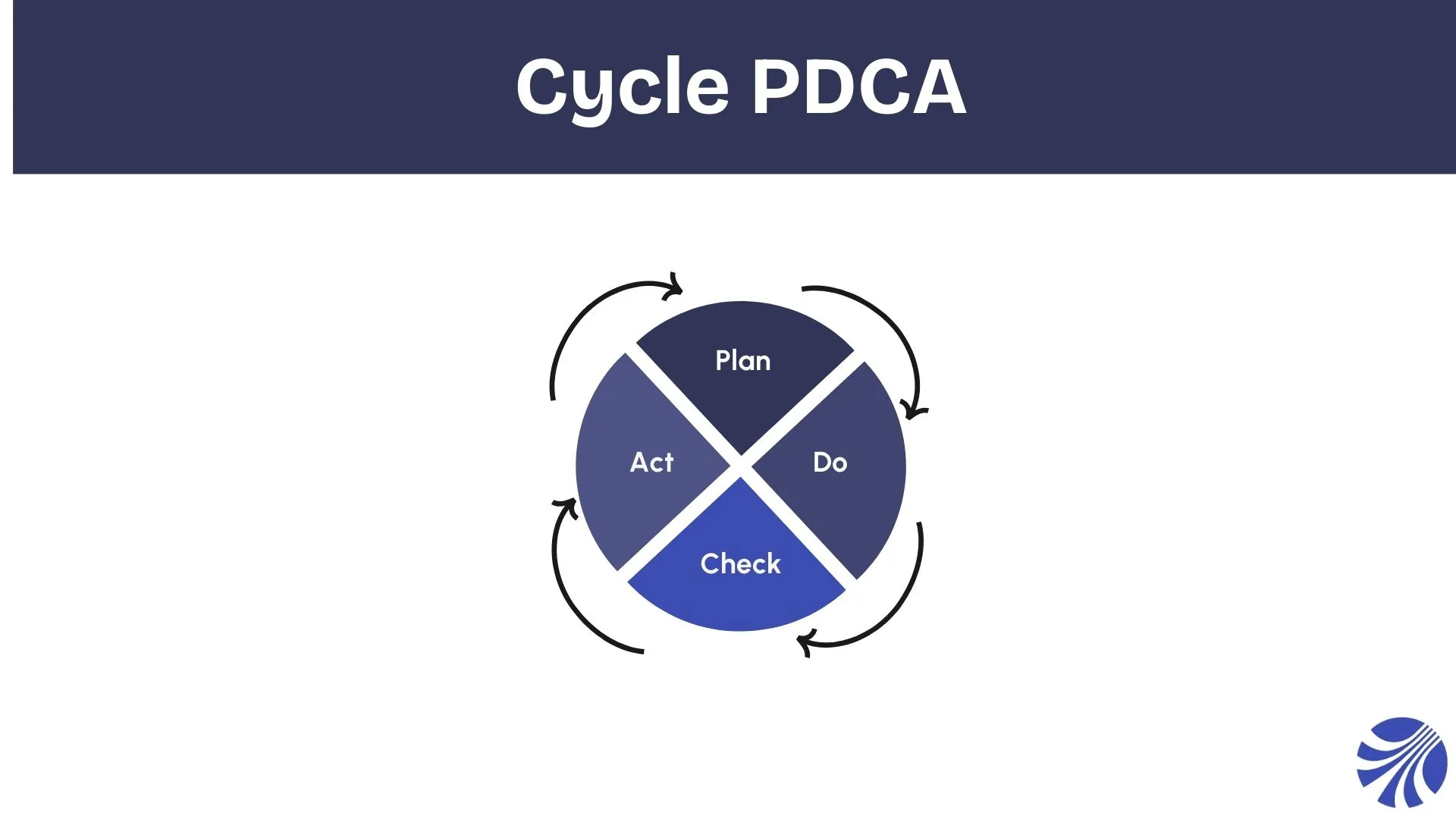
Le cycle PDCA, dont la représentation visuelle est appelée « Roue de Deming », est une méthode d’amélioration continue très usitée par les pôles qualité et gestion de projet des entreprises. C’est un sigle (plutôt qu’un acronyme) dont les lettres renvoient aux verbes anglais suivants : « Plan-Do-Check-Act ». Chacun d’entre eux constituant une des 4 étapes consécutives de cette méthodologie d’optimisation progressive d’un(e) :
- processus ;
- entreprise ;
- produit.
Le PDCA s’inscrit dans un cercle vertueux d'amélioration continue où chaque phase prépare la suivante, d’où le terme de “cycle PDCA”. Détaillons à présent les 4 étapes de l’approche :
Plan (Planifier)
Cette première étape vise à identifier le problème ou le processus à améliorer. Il s’agit de bien cerner la situation actuelle et de définir les objectifs.
Pour ce faire, on va mettre au point un plan d’action en se basant sur les données recueillies au sein du cahier des charges.
Yndia Dynamics peut vous aider à automatiser la collecte de ces données et fournir des estimations précises pour aider vos équipes à concevoir un plan d’action efficace. Notre solution logicielle facilite la phase de planification, notamment grâce à notre outil d’aide à la gestion de projet industriel.
Do (Exécuter)
Dans un second temps, on exécute le plan à petite échelle, autrement dit on l’expérimente. Cette étape de test vient confirmer ou infirmer les hypothèses précédemment formulées tout en réduisant les risques opérationnels.
Dans le cadre d’un projet de maintenance industrielle par exemple, on teste une mesure/ une action du plan sur une seule section de tuyauterie avant de l’appliquer à l’ensemble du réseau.
Dans l’optique de l’amélioration continue, ces tests pilotes forment un atout précieux car ils sont l’occasion d’ajuster le plan en fonction des premières observations.
Check (Vérifier)
Ensuite on conduit une analyse rigoureuse des résultats par rapport aux objectifs fixés à la première étape. Le check consiste ainsi à comparer les résultats réels aux attentes initiales et à éventuellement repérer des écarts trop importants.
On peut le faire grâce à différents outils de suivi aussi variés que :
- des tableaux de bord ;
- des audits internes ;
- des indicateurs de performance clés (KPI).
La régularité de ces vérifications des résultats est l’une des clés du cycle PDCA car cela permet de réagir promptement si les objectifs ne sont pas atteints.
Act (Agir)
Enfin vient la phase d’action où l’on améliore une fois de plus (c’est ça l’amélioration continue !) les solutions en fonction des retours d’expérience.
Si les résultats sont satisfaisants, les améliorations sont généralisées et standardisées pour toutes les équipes intervenantes.
Dans le cas contraire, on va revenir à la planification pour repenser le plan d’action et repartir sur un nouveau cycle d’amélioration PDCA.
Dans le cadre de projets industriels, l’étape Act est aussi le moment où l’on va documenter toutes les bonnes pratiques nécessaires au projet et les transmettre aux équipes via une formation afin de pérenniser les améliorations apportées pendant le cycle.
Avantages de l'approche P-D-C-A dans la gestion de projet
Le cycle PDCA est un processus itératif qui s’adapte sans problème à la gestion de projets de toutes tailles. Il permet aux entreprises de répondre efficacement aux attentes des clients en améliorant continuellement la qualité des services et des produits.
La flexibilité de la méthode fait que le PDCA est applicable à de très nombreux secteurs, allant de l’industrie manufacturière à la stratégie marketing. L’implication des équipes dans ce cycle favorise également la responsabilisation des parties prenantes et renforce l’engagement de tous vers un objectif commun.
Dans des projets ayant de très hauts standards de conformité réglementaire comme dans le secteur de la chaudronnerie, l’approche PDCA aide à identifier les goulots d’étranglement et à déployer des solutions qui répondent aux normes en vigueur tout en optimisant les ressources disponibles.
Utiliser l'outil PDCA dans vos projets : Stratégies et résultats
Comment mettre en place un PDCA ?
Dans le cadre d’un projet industriel, la planification peut concerner :
- les coûts ;
- les délais de livraison ;
- la satisfaction client, etc.
Pour ce faire, l’équipe doit s’appuyer sur des indicateurs précis et des analyses de causes profondes pour mieux comprendre les facteurs à l’origine des problèmes. Les outils Yndia Dynamics peuvent jouer un rôle central en facilitant la collecte des données et en améliorant la précision des prévisions.
Pour ce qui est de l’étape de l’exécution, dans un projet de soudage, le test pilote va par exemple consister à essayer de nouvelles techniques sur une partie de la chaîne de production. L’idée étant ici d’aligner méthode et ressources humaines et financières disponibles.
Dans la phase de check, en plus des outils comme les tableaux de bord, les audits internes, on peut recourir au diagramme d'Ishikawa pour évaluer les résultats. Sans oublier les indicateurs de performance (KPI) qui constituent un repère fondamental pour juger de l’efficacité du plan d’action.
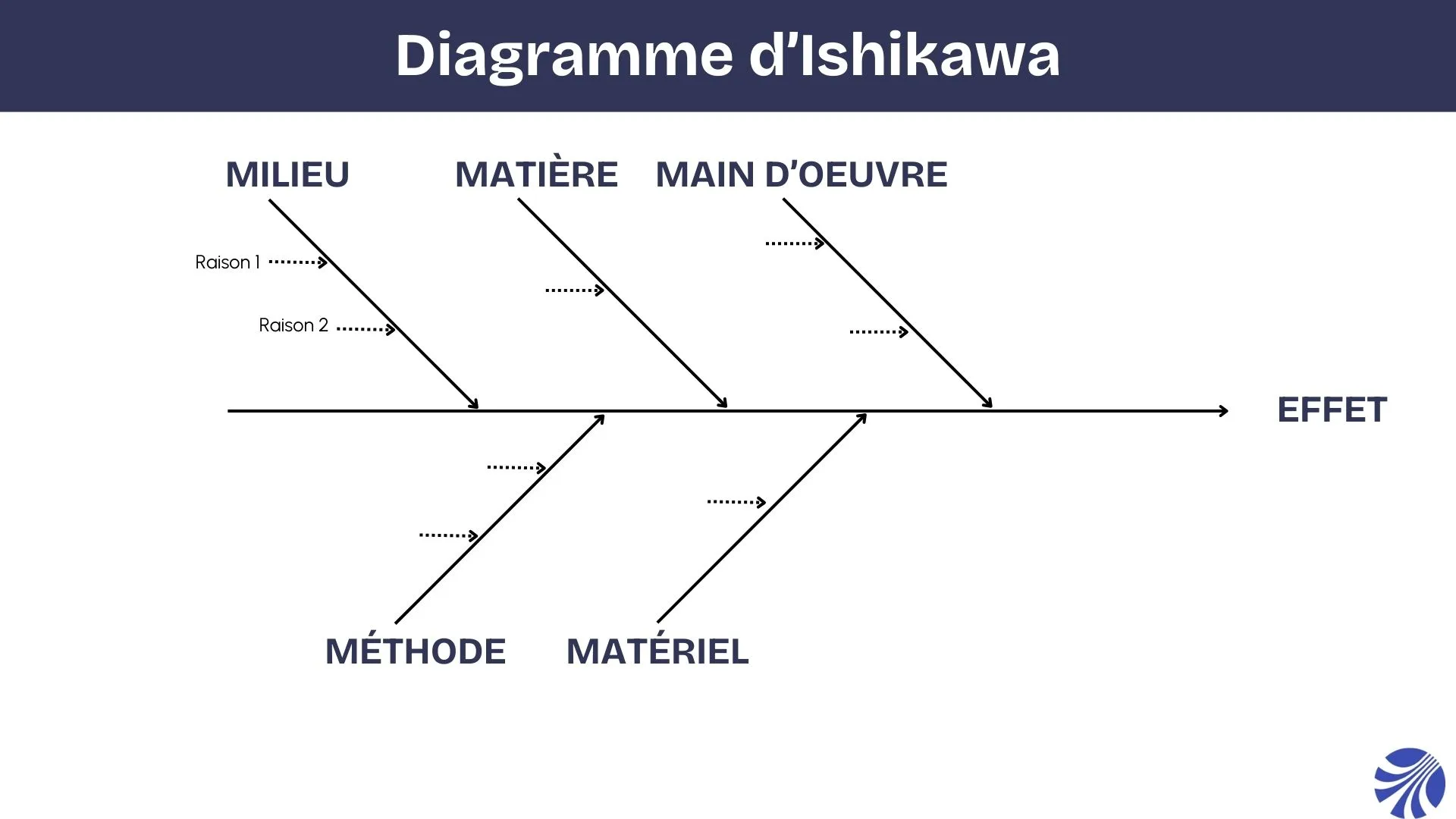
Enfin, dans l’étape Action, Selon les résultats du check, des ajustements peuvent être apportés pour renforcer l’efficacité de la solution. Si les résultats sont concluants, on va diffuser cette itération de la solution à toute l’entreprise.. Dans le cas contraire, un retour en arrière s’impose pour revoir le plan initial de fond en comble. Cette phase est essentielle pour filtrer les dernières erreurs et inscrire les solutions dans un cadre durable.
Exemple d’application du PDCA en tuyauterie industrielle
Plan : On identifie un problème récurrent de fuites au niveau des raccords et des joints dans quelques sections de tuyauterie de l’usine. Les arrêts de production nécessaires pour réparer posant problème, l’équipe fixe un objectif : réduire de 30 % les incidents de fuites dans le réseau de tuyauterie. Un plan d’action est arrêté : installer des capteurs de détection de pression pour anticiper les anomalies ; tenir à jour un calendrier de maintenance préventive des joints et raccords.
Do : L’équipe teste les mesures du plan sur une petite portion de la tuyauterie. En parallèle, les techniciens effectuent une inspection préventive plus fréquente des joints et remplacent ceux qui montrent des signes de faiblesse.
Check : Au bout de trois mois, l’équipe analyse les résultats. Elle observe une réduction notable des fuites sur la section de tuyauterie. Les capteurs ont détecté plusieurs anomalies avant qu’elles ne deviennent des fuites, ce qui a permis aux techniciens de remplacer les éléments défectueux sans nécessiter un arrêt complet de la production. Néanmoins on constate également que la fréquence de maintenance préventive peut être encore optimisée.
Act : Au vu des résultats, les membres de l’équipe décident d’étendre l’installation des capteurs de pression et le calendrier de maintenance à l’ensemble du réseau de tuyauterie de l’usine. Ils documentent cette méthode et la standardisent dans leurs procédures de maintenance. En cas de succès sur le long terme, ils envisageront d’intégrer ces pratiques dans la gestion de projets futurs pour les nouvelles installations de tuyauterie.
Le PDCA relève véritablement plus de l’état d’esprit que de l’outil. C’est un ensemble structuré de démarches qui convergent toutes vers un même objectif : l’amélioration continue des process et de l’entreprise. Tout le fonctionnement repose sur des itérations qui se succèdent en cycle, jusqu’à ce que certaines solutions soient jugées suffisamment adaptées pour être érigées en bonnes pratiques standardisées. Mais même dans les cas où le cycle ne recommence pas à la première étape, le travail de veille et de suivi de performance doit continuer afin de repérer les écarts entre objectifs et résultats.
Grâce à nos solutions innovantes de collecte et d’analyse de données, chez Yndia Dynamics, nous vous aidons à appliquer la méthode PDCA pour une performance durable et une amélioration continue. Découvrez nos outils !